Build Ahead
Embracing a Modular Industry Reboot: Standardization for a Dynamic Future
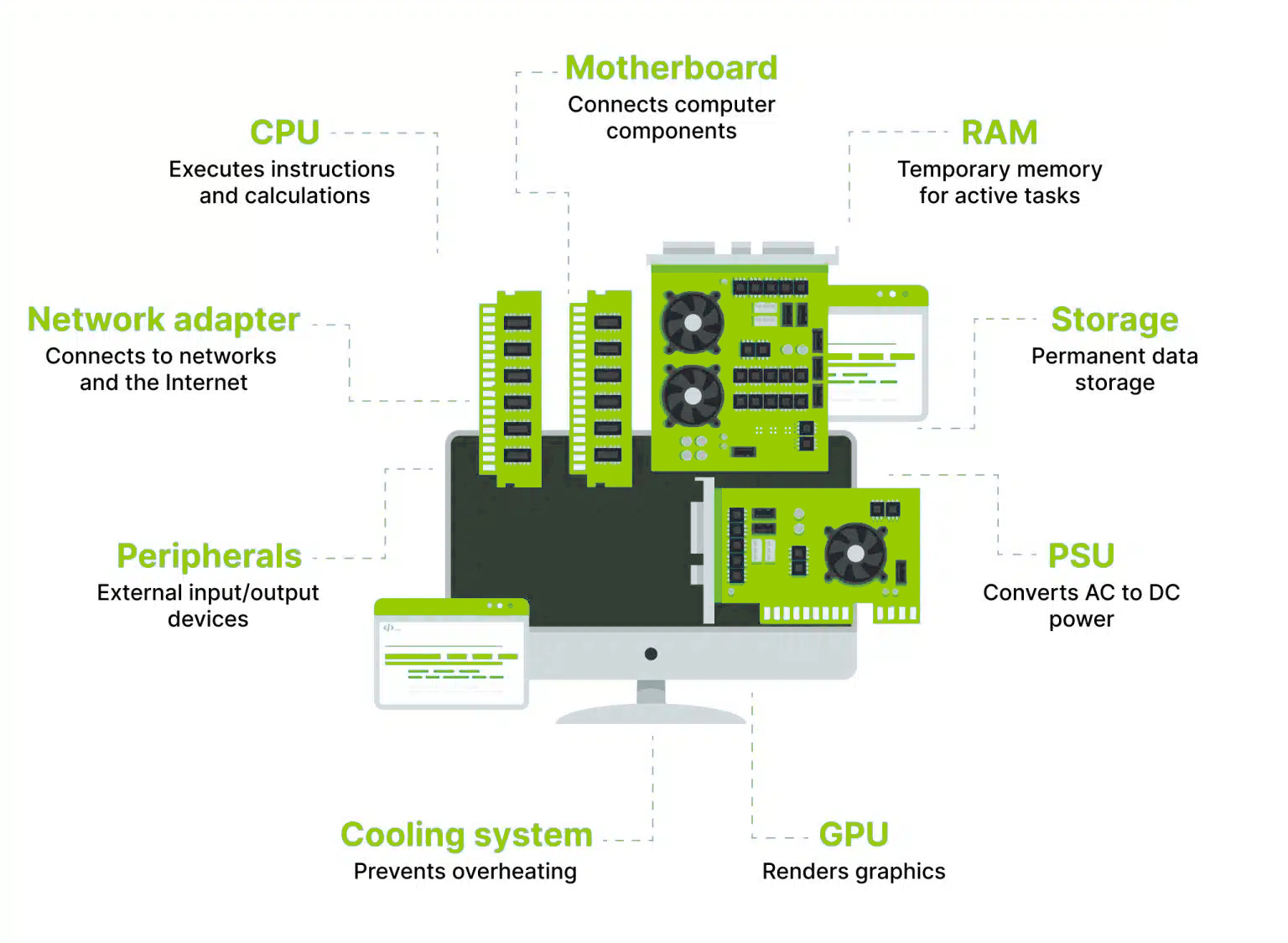
The North American modular construction industry is at a crossroads. While custom and production modular homes each hold significant roles in the housing landscape, the current market shift demands something new—a strategy that allows modular to scale beyond its current niche and serve broader segments. Ken Semler aptly captures this need in his call for an “industry reboot” where modular manufacturers adopt standardized components that other companies produce, enabling agile, cost-effective assembly tailored to various markets. We wholeheartedly agree: there’s no reason this approach can’t work for modular manufacturing, and now is the time to embrace it.
Semler’s vision is grounded in practicality. Historically, modular construction took root in the Northeast, where custom single-family homes required flexible design and high-end finishes. To serve this custom market, manufacturers built design teams capable of producing unique, client-specific designs—an approach that comes with high overhead and limits scalability. But as the modular industry reaches a point where scaling is essential to growth, these custom models can’t alone meet the demand from single-family developers for high-quality, budget-conscious homes produced at scale.
To transform modular construction into a mainstream solution, we must shift to a mass-customization model, one that uses standardized sub-assemblies and allows final configuration late in the process. Dell Computer did it in the ‘90s, as Semler points out. By outsourcing components and focusing on final assembly, they reduced inventory and cut costs while maintaining customization and quality for both individual customers and corporate accounts. Similarly, in modular manufacturing, a factory producing wall panels, roof sections, or bath pods—interchangeable, high-quality components—can streamline the process, keeping overhead low and flexibility high. This allows custom builders and developers to get what they need: rapid, quality construction without the bottleneck of a fully custom design and manufacturing pipeline.
Standardized components are not a limitation; they are an invitation to innovation. These modular “building blocks” can be assembled in numerous configurations, giving developers the flexibility to customize layouts while preserving the efficiencies of a streamlined production line. More importantly, this approach enables modular to meet the cost needs of the developer while still appealing to custom clients who want bespoke homes. Developers will benefit from reduced timelines and predictable costs, and custom builders will have access to high-value components without losing the flexibility of unique design elements.
The benefits extend beyond the immediate stakeholders. Embracing this reboot will allow modular construction to play a critical role in tackling broader challenges: from addressing the housing crisis by offering scalable, affordable options, to meeting sustainability goals through efficient, waste-reducing offsite production. With a robust, standardized component model, modular construction could deliver homes that are adaptable, energy-efficient, and built to last.
At the Center for Offsite Construction, we see this reboot not just as a solution to current challenges but as a strategy for an enduring, resilient industry. It’s time to broaden the market for modular, to scale efficiently, and to make modular construction the agile, innovative answer to modern housing demands. This approach isn’t just possible; it’s essential. And like Semler, we’re confident that the modular industry is ready to take the leap.
More Posts
All Posts